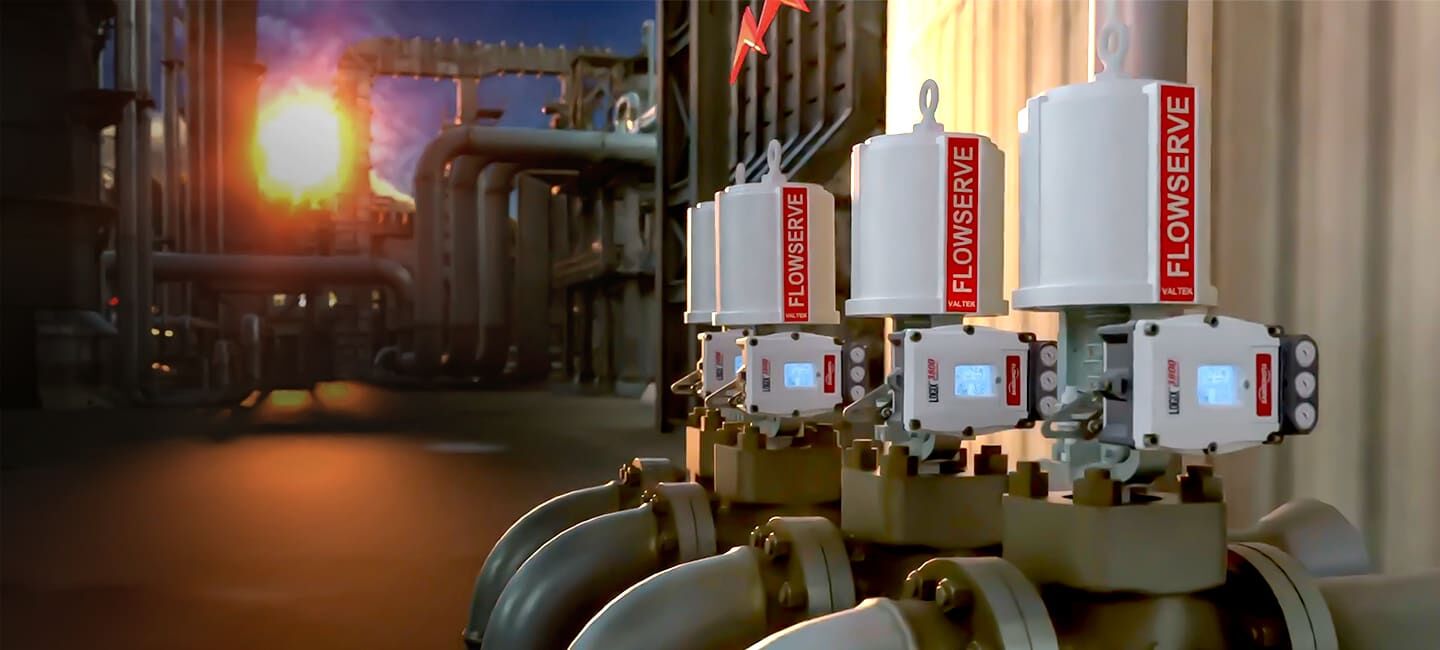
Quickly Shipping Valtek® Mark One™ Control Valve Ends Oil Producer’s Leak Risks
Challenge
A leaking control valve in a critical system at a leading Canadian oil sands producer’s facility created a significant environmental, health and safety hazard. Plant operators contacted Flowserve seeking an immediate replacement valve to minimize disruption to operations and eliminate leakage risks.
Solution
Flowserve sales engineer based near the company’s location coordinated with the Flowserve Quick Response Center in Edmonton, Alberta, to assemble and test a bare stem valve that met all of the oil sands producer’s requirements. Within five hours of the initial call for support, Flowserve and its Quick-Ship Program team had a Valtek Mark One control valve assembled, tested and ready for shipment to the customer. Quickly Shipping Valtek® Mark One™Control Valve Ends Oil Producer’s Leak Risks.
Urgent call for help to stem a leaking valve
Operators at an oil sands processing plant in western Canada discovered a leak in a globe-style control valve in a critical system that removes sand and water and upgrades thick bitumen into a crude oil that can be refined. Corrosive and abrasive process conditions had created a small hole in the control valve, causing process fluids to leak. A replacement valve would be needed to eliminate the leakage and avoid significant environmental, health and safety risks. About midday, plant operators called a Flowserve sales engineer who is based less than an hour away from their plant. They needed to know whether a replacement valve might be available and how long it may take to deliver it to their facility.
Replacement shipped in one afternoon
The sales engineer immediately contacted the Flowserve Quick Response Center (QRC) in Edmonton, located about four hours from the oil sands plant. The Flowserve network of QRCs is staffed by engineers and specialists available for just such an emergency. They’re also stocked with valves and components in order to meet the tightest deadlines, restore valves to near original quality, and repair or replace a wide variety of valve styles. In this case, the Edmonton QRC had in stock a WCC (carbon steel) Mark One globe valve body the customer needed. Additional parts to produce a bare stem valve that matched the oil sands plant’s requirements also were in inventory. By 4:20 p.m., Flowserve had assembled and tested the Mark One valve and notified the customer that it was ready to be shipped.
Avoid downtime with rapid response
Flowserve QRCs are equipped to provide emergency responses like the one experienced by the Canadian oil sands producer. In more routine circumstances, the Valtek Mark One Control Valve Quick-Ship Program provides customers with Flowserve-tested Mark One valves anywhere in North America in one week or less. In many cases, Flowserve can deliver valves within 24 to 48 hours so customers can reduce downtime and keep operations moving. In contrast, standard industry lead times for valves can be anywhere from four to 12 weeks.
Flowserve network provides 24/7 emergency support
Flowserve understands how critical it is to have a trusted partner that will offer fast service and quality products to keep facilities up and running. This is why Flowserve QRCs provide the highest level of service, including 24-hour emergency service and on-site repair with mobile units. Flowserve service technicians can be on-site in any North American plant within 24 hours.
Core QRC capabilities include:
- Control valve repair
- Actuation repair
- Valve automation
- Remanufactured valves
- Field service and on-site repair
- Oxygen cleaning
- Full machine and weld shops
- Turnaround management
- Plant surveys
Read the whole story here via Flowserve: