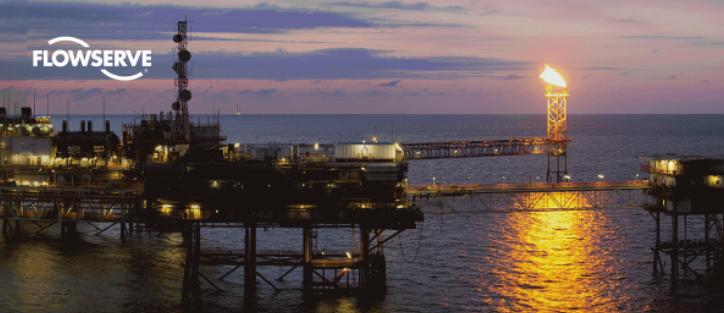
Next-Generation Liquid Ring Compressors
Updating 100-year-old technology for the next generation
Liquid ring vacuum compressors are a proven solution widely used across process industries, especially for the recovery of gases and vapors.
They are utilized in applications where severe conditions exist and safety is a critical requirement. Demand for this equipment is expected to continue to grow at nearly 5% a year through 20291 because liquid ring compressors offer reliable solutions in refinery applications that recover flare gas. Liquid ring compressors also are ideal solutions for specialized applications such as chlorine or hydrogen compression and in the production of vinyl chloride monomers, biodiesel or ethanol, and other transesterification processes.
Liquid ring compressors can use any kind of service liquid to create a seal, making them ideal for applications in which process contamination is prohibited. The most common service liquid is water, which combined with the fact that the compressors are engineered with only one moving part, provides efficient operation and a long lifecycle with less downtime and maintenance costs.
While liquid ring technology has been available for more than 100 years to meet a range of capacity requirements, the next generation of compressors from some manufacturers can provide full compliance with the existing and expected updates of the API 681 standards for the chemical, gas and petroleum industries. Learn more in this white paper about liquid ring compressor advancements and how to incorporate the equipment cost-effectively into your recovery processes.
Ideal for demanding industrial processes
The main applications for liquid ring compressors include flare gas recovery and processing of especially aggressive, flammable or corrosive gases and vapors found in:
- Chemical processing
- Chlorine compression
- CO2 treatment
- Ozone bleaching
- Vinyl chloride monomer (VCM) or aromatics recovery
- Water treatment
Key Processes:
- Batch reactors
- Deaeration and gasification
- Gas compression
- Flare gas recovery
- Off gas recovery
- Vent gas compression
- Vapor recovery
How liquid ring compressors work
with a service liquid (typically water).
2. The rotation creates centrifugal force that forms a moving ring of fluid
against the interior wall of the casing.
3. This results in a volumetric expansion in the outflowing section of the
liquid ring, which causes the gaseous process medium to be drawn in
via the inlet port in the guide plate.
4. In the inflowing section of the liquid ring, the volume is reduced,
compressing the medium.
5. After compression, the medium is discharged via the outlet port in the
guide plate together with the service liquid.
The medium being pumped comes into contact with the service liquid,
thus allowing these media to affect each other.
Proven liquid ring performance
Some compressor technologies can become unreliable when liquids, particles (debris) or vapors are present in the process medium. Liquid ring machines efficiently handle the process gases, which will be separated from the unwanted liquids or vapors and recirculated or recovered.
Comparing compressors for flare gas recovery
Liquid ring compressors are preferred for flare gas recovery applications because of their high reliability and low initial and maintenance costs.
Compressor design enhances performance
The rotors of some liquid ring compressors available today have been designed with an increasing hub diameter for maximum loads in terms of bending load and intrinsic frequency. Any axial loads are absorbed by oil-lubricated bearings. The bearing clearance is kept as short as possible to prevent shafts bending under any operating conditions.
Other features to consider when evaluating which compressor best matches your process requirements include:
Isothermal efficiency
The vanes of each impeller inside a liquid ring compressor are curved for optimum energy transfer.
As the compression power is derived from the energy generated by the rotary movement of the liquid ring, the
amount of energy it contains should be at least equivalent to the isothermal compression rating. The design supports stable liquid ring conditions over the full available pressure ratio between inlet and outlet pressures. Internal guides for the service liquid minimize internal losses on the axial sealing surfaces between the impellers and guide discs. Overflow losses are thus significantly reduced.
As a result, isothermal efficiency is improved by as much as 23% while also reducing power consumption.
Radial forces
A second stage is used on some compressors to manage high differential pressure. The center body of this stage is designed so that the liquid ring flows into and out of the impeller blade cells twice during each revolution of the impeller. This ensures that radial forces are avoided, and shaft deflection is minimized in order to reduce vibrations, which can negatively affect efficiency and service life.
Variable gas outlet temperature and water consumption
Water for cooling can be kept to a minimum with liquid ring compressors and a system of pre- and after-coolers. Temperature control also can ensure that components in the medium do not harden and block the processing system.
After the mix of gases and liquids has been discharged from the compressor, the liquids can be removed from the gas in a separator and reused as service liquid after having been cooled. Cooling is necessary because most of the heat generated during compression and the various condensation processes is absorbed by the liquid. Some of these compressors can manage service liquid flows from 200 l/min up to 400 l/min. The compressors also react predictably to different amounts of water to keep compression performance
stable. This ensures effective heat dissipation and control of the outlet temperature.
Cast versus welded parts
Higher performance and reliability are achieved by casting the main parts such as casings and impellers instead of welding them. Cast materials show more rigid behavior compared to welding constructions. In addition, welded parts must be inspected through radiographic examinations and dye penetrant tests to confirm they comply with API 681 standards. You can avoid these costly and time-consuming quality checks with cast parts.
Be sure to ask manufacturers how they design and test their castings. Some compressor manufacturers engineer their machines based on the results of casting simulation. This makes it possible to visualize mold filling, solidification and cooling, and predict the location of internal defects such as shrinkage porosity, sand inclusions and cold shuts.
Discharge connections on left or right
Look for liquid ring compressors with a discharge connection on the shaft level that can be connected on the left or toward the right side of the casing. This saves space and enables several machines to be arranged face-to-face or back-to-back on a skid. The compressors can be set in all positions by changing the location of the discharge flange.
Casing designs that position the discharge connection at shaft level also help technicians avoid overfilling the compressor at startup. A machine completely filled with liquid can be damaged by deformation of the shaft and impeller cells.
Reduced vibration
Some designs for liquid ring compressors shrink the distance between the shaft bearings and the attachment points on the feet of the machine to a skid or the floor. Deflection and amplitude during operation are reduced while the elastic vibration behavior of the compressor is positively influenced. As a result, vibration is reduced. This prevents excessive material stress, premature aging, and damage to bearings and mechanical seals.
Integrated rotor support
Look for liquid seal compressors with mechanical seals designed to include an internal rotor support, which enables easy access to the bearings for service. The seal is designed to carry the static rotor weight. Other designs require technicians to disassemble the compressor on-site, disconnect the piping, and lift the machine with a crane for transport to an off-site repair center. To reduce downtime and costs, look for a liquid ring compressor with integrated rotor support to change bearings on-site.
Look for computational support and engineering experience
Modern compressor designs are calculated down to the component level using finite element methods (FEM) to better understand fluid behavior and thermal transport. The physical effects of different processes and working points can affect compressor performance and service life. FEM results can be used to achieve weight reduction and determine the best possible use of the available space. Therefore, it’s critical that FEM data be analyzed and the insights they yield be implemented into a safe and durable compressor construction.
Conclusion
Modern liquid ring compressors meet the API 681 standard with a rigid design verified with modern simulation tools. They also incorporate energy-efficient design features that lower water consumption and save space in facilities for petroleum, gas, chemical and general processes.
Higher performance, reduced maintenance and repair costs, and a longer service life result from liquid ring operating principles. A rotating impeller is eccentrically mounted within a round center casing. Service liquid is centrifuged into a uniform liquid ring around the circumference of the center body. Liquid volume between each of the impeller blades varies as the impeller rotates. This creates a reciprocating piston action on the gas contained within each of the blade sections. As volume increases, vacuum is created; as volume reduces, compression occurs.