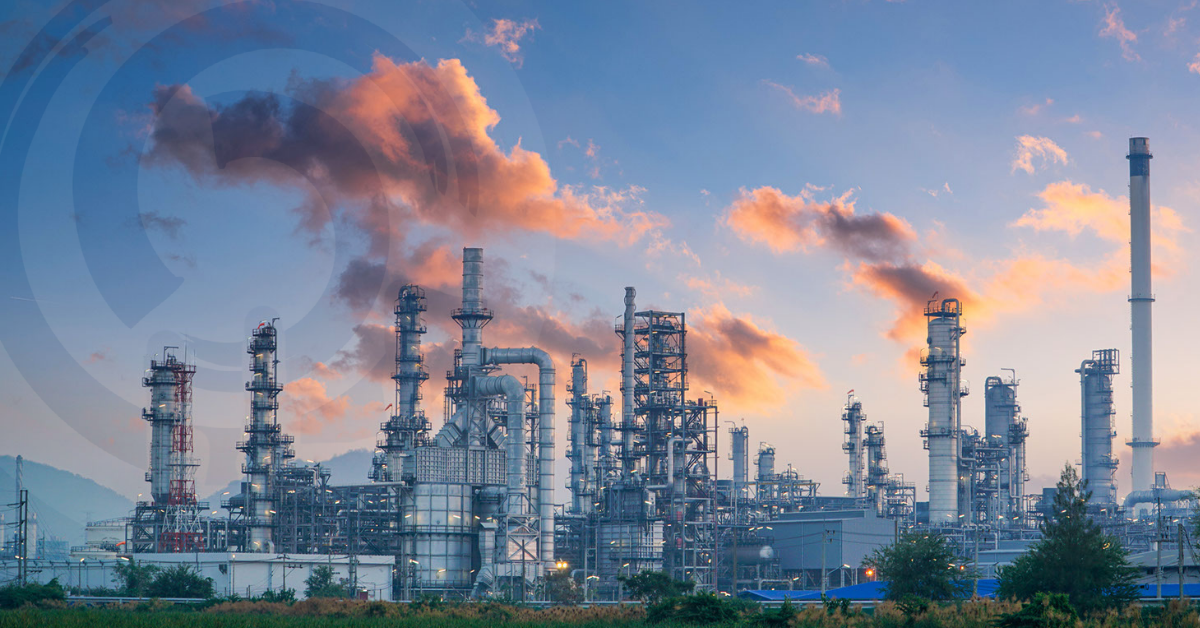
How Seals Can Protect Your Operation and the Environment
When you’re designing facilities and systems to handle your unique processes, or you’re planning to retrofit or upgrade existing plants, there are critical considerations about how you will seal rotating equipment. Overlooking them early in a project can jeopardize whether your company achieves its objectives for efficiency, safety, environmental compliance, energy transition and, yes, profitability.
So I recommend prioritizing your project planning time to ask and answer the following five big questions. Let’s look at how your answers to these questions and the decisions your company makes upfront can ultimately influence your project’s success.
1. How will your sealing strategy maintain boundary integrity?
This first question really should focus your team on what you intend to accomplish. Mechanical seals on compressors, mixers, pumps and turbomachinery enable plant operators to implement and operate process systems that:
- Enhance reliability
- Consume less water and better manage other resources
- Control fugitive emissions and ensure environmental compliance
- Minimize or eliminate leakage
- Reduce energy consumption and costs
- Simplify maintenance and repairs
- Tolerate a broad range of conditions such as hot or ultra-cold temperatures, high pressures and solids-laden process fluids
2. What rotating equipment will be specified, and how will it be utilized in your processes?
Mechanical seals are a proven solution for more than just pumps. There’s a broad range of rotating equipment used across industries and processes to consider, such as:
- Agitators
- Augers
- Autoclaves
- Ball mills
- Blenders
- Blowers
- Centrifuges
- Compressors
- Conveyors
- etc…
Look for a partner such as Flowserve with deep experience beyond pump seals where designing, building, testing and implementing seals compliment the unique characteristics of various rotating equipment.
3. What are your specific processes in which mechanical seals are needed?
Start with your application and then research the seal design options that ideally match your requirements. Here are some examples:
Application Considerations
- Pressure, temperature, fluid type
- Higher pressure, clean fluids
- High temperature, contamination
- Abrasive solids
- Pressure, economy
- Speed, equipment run-out
- Installation ease, fitment
- Wet, dry, multiphase
- Chemical compatibility
- Leakage mitigation
- Zero or low emissions
- Vapor margin, hot water
Seal Design Options
- Pusher or bellows
- O-ring or gasket pusher
- Welded metal bellows
- Elastomer spring
- Balanced or unbalanced
- Flexible stator or rotor
- Cartridge, component or split
- Boundary lubricated or lift-off
- Materials of construction
- Single, dual or triple
- Dual pressurized or unpressurized
- Face topography
4. How can piping plans enhance reliability?
There are so many piping plans available for mechanical seal systems that it pays to spend extra time and attention early in your facility design process. The goal should be to specify a piping plan that best matches your application so it addresses every requirement; it also should minimize unplanned downtime and extend equipment lifecycle. Be sure to consider how a piping plan will improve the mechanical seal environment by:
- Altering seal chamber pressure
- Capturing, detecting and/or preventing leakage
- Cleaning the process fluid
- Controlling the atmospheric side
- Flushing to remove heat
- Increasing the vapor pressure margin
- Introducing external fluid
- Isolating from process fluids
- Lowering the fluid temperature
- Providing an environment of barrier/buffer fluid
5. What are the right components within the piping plan?
Again, there are so many options from which you can choose that companies can benefit by partnering with mechanical seal experts. You’re not alone (or don’t have to be) when considering seal support system components. At Flowserve, our application and product engineers understand when and how to use components, including:
- Barrier fluids
- Barrier reservoirs
- Bladder accumulators
- Circulators
- Flush controllers
- Gas boosters
- Gas conditioners
- Finned pipe coolers
- Forced draft coolers
- Instrumentation (indicators, switches, transmitters)
- Leakage collectors
- Piston accumulators
- Shell and tube coolers
- Solids separators
Defining and achieving your project goals
There are certainly more questions to ask, but answering these first five thoughtfully and thoroughly will get your project team off to a strong start. I’m confident they’ll also lead you to discover the additional considerations appropriate for the facility and processes you envision.
Exploring all the options raised by answers to these questions will enable you to take the next essential step toward successfully completing your project. This entails assessing whether the goals of your engineering, procurement and construction (EPC) consultant, original equipment manufacturers (OEMs) and company are tightly aligned.
Confirming alignment requires making sure all stakeholders and partners know the challenges you need to overcome. They must understand in detail both current conditions and expected outcomes. And you need to be certain they agree the proposed mechanical seal solutions will deliver reliability improvements, energy reductions and every other objective your company has identified for the facility and processes you’re planning.
If all parties don’t know, understand and agree on whether a mechanical seal option can get the job done, keep asking questions.