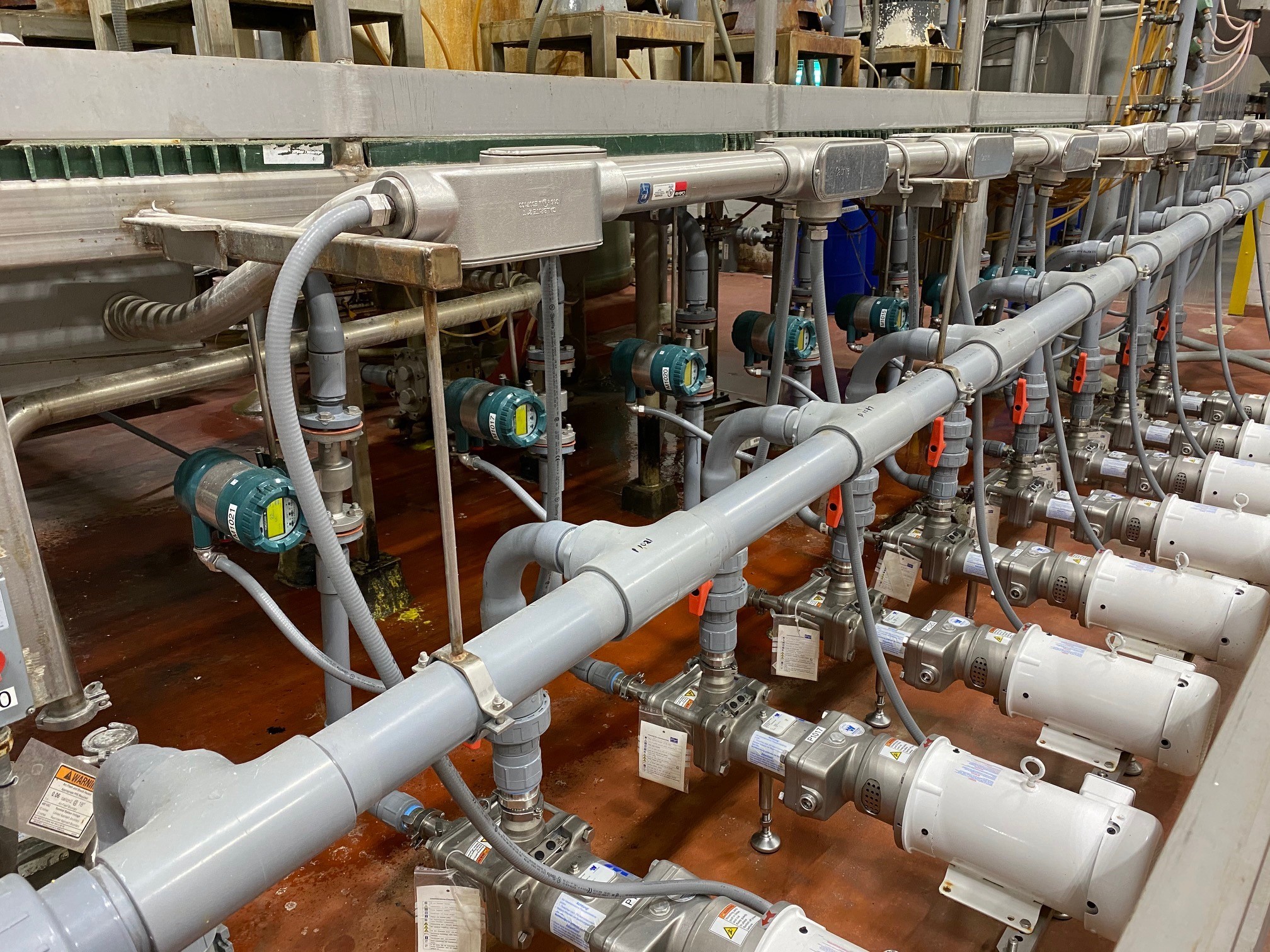
Simplified and Accurate Flowrates Preserve Equipment Health
Plant Name: Condiment Producer
Industry: Food and Beverage
Product(s): Mustard and Condiment Line
Application
As part of the mustard-production process, industrial grinders crush and blend ingredients including mustard seeds and water. The result is a slushy material that moves through pipes to the next phase in the process.
If a grinder runs dry or becomes blocked, operators might need to slow or halt production. A magnetic flowmeter (magmeter) measures the flow of material into and out of the grinder. To stay alert for process conditions that might damage the grinder or negatively impact the downstream process, operators can interface magmeters with a process control system or they can monitor flowrates manually.
Challenges
Providing accurate measurements in the slushy material flow is difficult for conventional magmeters. With the addition of heavy vibration from the nearby process equipment, many flowmeters are not rugged enough and cannot provide a stable flow measurement under these conditions.
Rather than risking the grinders at the heart of their eight mustard lines, the operators manually monitored the flow around the grinders to ensure they would not be damaged. The producer knew they would save time if they could implement a reliable flowmeter solution, but the demands of the application left them with no identifiable solution at the time.
After operating for several years without flow measurements, the condiment facility decided the risk to the equipment and the cost of manually monitoring was too high. An instrumented solution needed to be identified.
Solution
The condiment facility staff had success with Yokogawa’s ADMAG TI AXG magnetic flowmeters in other applications. When they learned EtherNet/IP communication was now offered on the ADMAG TI – AXG, they chose to use the Yokogawa magmeter solution on the mustard grinding lines.
From the beginning, the mustard team found that set-up and digital integration of the magmeters were simplified by an intuitive interface that was accessible through the EtherNet/IP communications. This also enables the magmeters to display flow information where it is best accessed by the operator — in the field or via an interface in the control room. The easy access to flow information allows the operators to be more responsive to process situations and preserve the health of the grinding equipment.
Even in the slushy material, flow measurement was reliable thanks to Yokogawa’s proprietary dual-frequency excitation method that combines traditional high and low-frequency excitation. The combination ensures greater stability and quicker response even when noise or other problems are present in the line.
The ADMAG TI has a built-in totalizer that simplifies tasks. No extra programming is needed and the totalizer can be reset via a PLC command over the network. This capability reduces errors and eliminates the need to recalculate or track over time.
The facilities maintenance team has found that the ADMAG TI handles the viscous material well and requires very little attention. This means they are not only saving the grinder from problems, but they are also saving maintenance time and reducing parts inventory.
Key Advantages
- Reduced risk of grinder problems thanks to reliable flow measurements
- Easy installation with flexible options and intuitive set-up
- Quicker operator response through easy access to flow information from the plant floor to the control room